Steel is one of the most useful metals in various industries. It is used in the automotive industry, to manufacture ships, trains, in the health sector, household appliances, tools, components, and much more.
How to work steel plates?
Such versatility has led to the emergence of various techniques. These techniques allow the steel plates to be worked to mold them to the needs of each industry, including bending, welding, drilling and cutting, techniques that make it possible to obtain shapes and sizes according to a specific project.
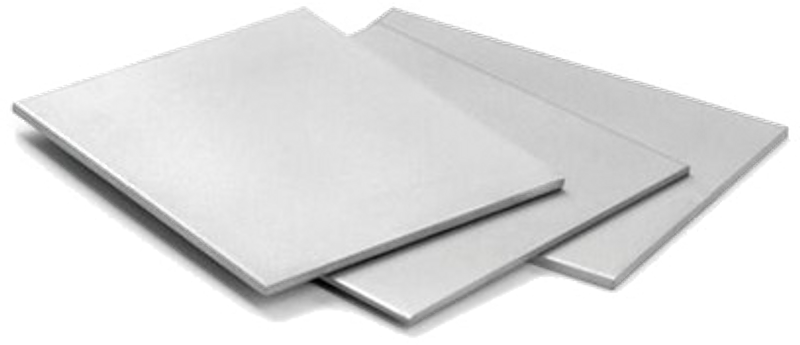
Steel plate cutting methods
To apply cuts to the steel plate, several techniques can be automated or manual, and that will depend on the characteristics of the plate in terms of thickness or length.
Here are mentioned four methods:
Cutting with oxygen
It is made using an oxyfuel torch, which is ideal for working on a very thick angle bar. This method is one of the oldest and is a low cost since the equipment, and all the material is very economical. Similarly, the process is quite simple.
The cutting surfaces derived from this technique are smooth, with little waste on the edges, which is thanks to the preheating flame and the proper adjustment of the torch.
Its use is recommended for plates thicker than 1 inch, and cuts can be made with several torches at the same time.
Plasma cutting
It is enhanced with plasma equipment, which is usually more complex than a torch. The cuts on the chequered plate are much faster and are perfect as long as the bale is neither too thin nor less than 6.4 mm nor too thick or greater than 38.1 mm.
It is a method that generates greater productivity, which compensates the cost of the equipment in a very short time.
Laser cutting
This technique is ideal for steel pipe whose thickness does not exceed 31.88 mm so that the work goes well. The adjustments must be exact, which implies purity of the gas, quality of the beam, state of the nozzle and that the steel is indicated for laser.
We are not talking about a fast cutting process since it depends on the chemical reaction between oxygen and iron. However, it is a very exact method using which fairly precise contours, small holes, and very well finished, the quality of the edges is excellent, little slag, and very perpendicular edges.
This is a process that generates a lot of confidence, and the level of automation of the machine allows most flat bar cuts to be executed without human intervention.
Water jet cutting
Through this process, exact cuts are achieved and quite smooth. One of the great advantages of this technique is that there is practically no limitation linked to the thickness of the hollow section, except for those plates that exceed 203.2 mm since the water jet tends to diverge.
It also allows us to make cuts through the use of several heads. Of course, each head requires its additional water flow with a smaller hole or a larger pump.
No comments:
Post a Comment